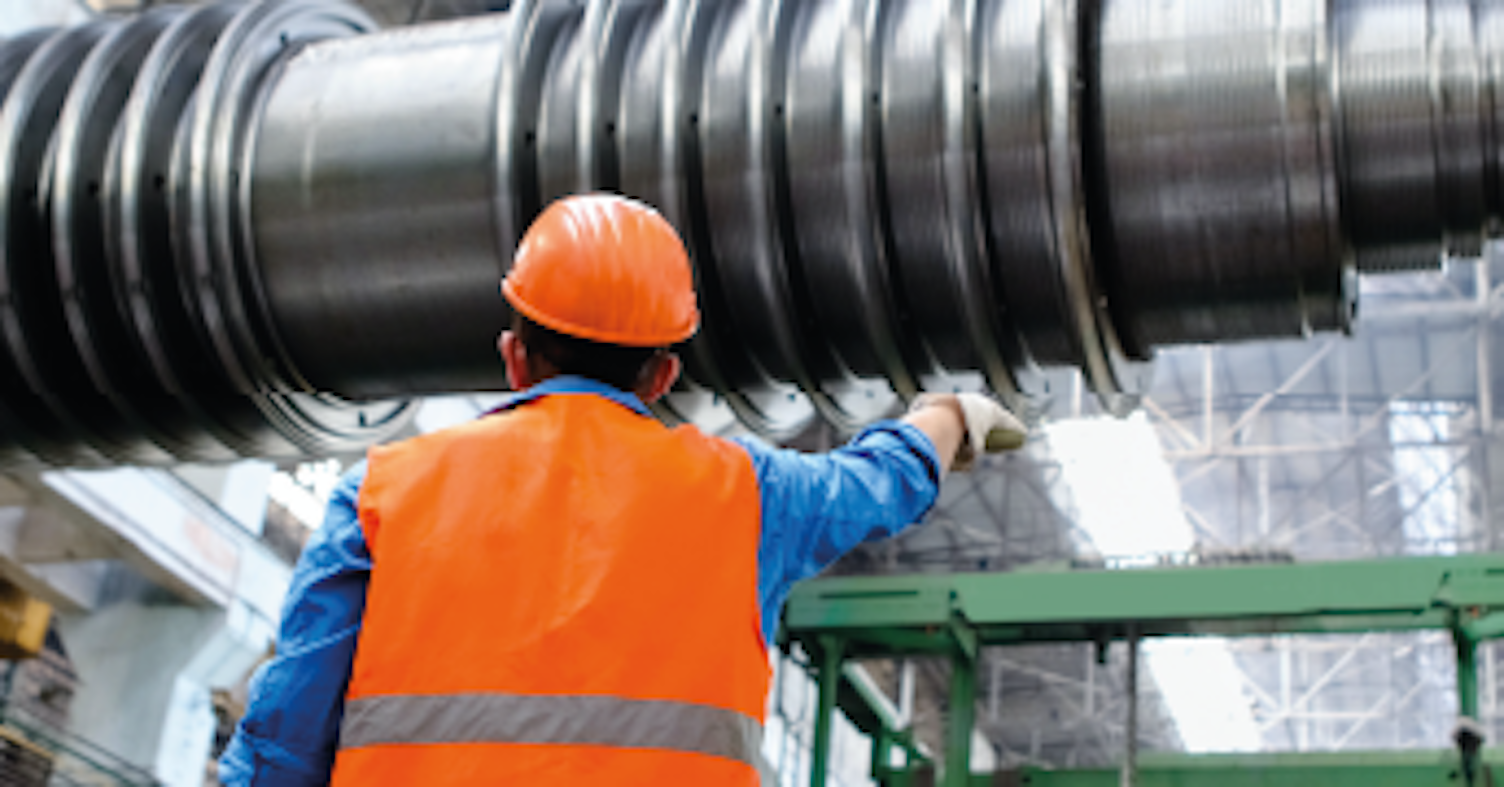
Parte integrante da metodologia Lean, o “Single-Minute Exchange of Die” (SMED) é uma ferramenta de gestão desenvolvida também no Japão, por Taiichi Ohno, pai do próprio Lean e do Sistema de Produção da Toyota, o seu maior caso prático.
Autor:
Rui Ferreira
Director de Produtividade da SGS Portugal
Em que consiste o SMED?
O SMED concretiza-se na redução do tempo necessário para efetuar determinada mudança de configuração num equipamento inserido numa linha de produção
O principal objetivo do SMED passa, então, por alterar processos no sentido de permitir que o maior número de passos de conversão possam ser tomados ainda com o equipamento em funcionamento, para reduzir eventuais períodos de paragem e minimizar os impactos na restante linha de produção. A estratégia foi aperfeiçoada por Shigeo Shingo e, de acordo com alguns casos de estudo, os tempos de transição podem ser otimizados em até 94%. Um dos objetivos declarados do SMED é o reduzir tempos de transição entre equipamentos (ou das suas diferentes configurações) a menos de 10 minutos.
O SMED preconiza o processamento das transições em etapas e faz uma divisão entre elementos “internos”, aqueles que só podem ser completados com o equipamento efetivamente parado, e os “externos”, todos aqueles que podem ser executados em paralelo, enquanto o equipamento ainda se encontra em funcionamento.
Quais os benefícios do SMED?
O SMED permite a redução dos custos associados à produção, nomeadamente pela maior flexibilidade do sistema, e pela consequente otimização dos tempos de produção e prazos de entrega — estas são algumas das principais razões que enquadram o SMED na metodologia Lean e que têm um impacto claro na satisfação do cliente.
O facto de permitir rápidas mudanças à linha de produção significa também a possibilidade de produzir lotes menores, ao invés da produção de grandes quantidades de stock para aproveitar uma determinada configuração dos equipamentos. Simultaneamente, isto traduz-se numa menor quantidade de stock de matérias-primas, reduzindo uma vez mais os custos adjacentes à produção.
Origem da designação
Como referido, o termo “Single-Minute Exchange of Die” nasceu na Toyota, e a designação contemporânea do processo é ainda testemunha da sua origem. Por “dies” entendem-se as maquinarias de grandes dimensões que moldam as diferentes partes de um veículo e que, por isso, tinham de ser trocadas para cada modelo em produção. Estas máquinas, de grandes dimensões e várias toneladas, exigiam uma montagem perfeita para garantir a correção e qualidade do produto, registavam tempos de transição que podiam ir de doze horas até três dias. Os impactos negativos de uma tal paragem eram compreensivelmente elevados. Por meio da análise e introdução de sucessivas melhorias, como a calendarização das mudanças de equipamento, mas também através da adoção de novas soluções tecnológicas, como instrumentos de medição, os engenheiros da Toyota conseguiram reduzir esse período para menos de dez minutos (o tal conceito de “single-minute”, no sentido de apenas um algarismo), oferecendo grandes poupanças e flexibilidade às suas linhas de montagem.
Se pretende saber mais sobre Lean Manufacturing, descubra os nossos cursos >>
Para mais informações ou inscrições, por favor contacte:
tel: 808 200 747 (Seg. a Sex. das 9h às 18h)
@:pt.info@sgs.com
SOBRE A SGS
Somos a SGS - a empresa líder mundial em testes, inspeção e certificação. Somos reconhecidos como a referência mundial em qualidade e integridade. Os nossos 96.000 colaboradores operam numa rede de 2.600 escritórios e laboratórios, e trabalham em conjunto para possibilitar um mundo melhor, mais seguro e interligado.
Polo Tecnológico de Lisboa,
Rua Cesina Adães Bermudes, Lote 11, 1600-604,
Lisboa,
Portugal